Transport of highly sensitive goods
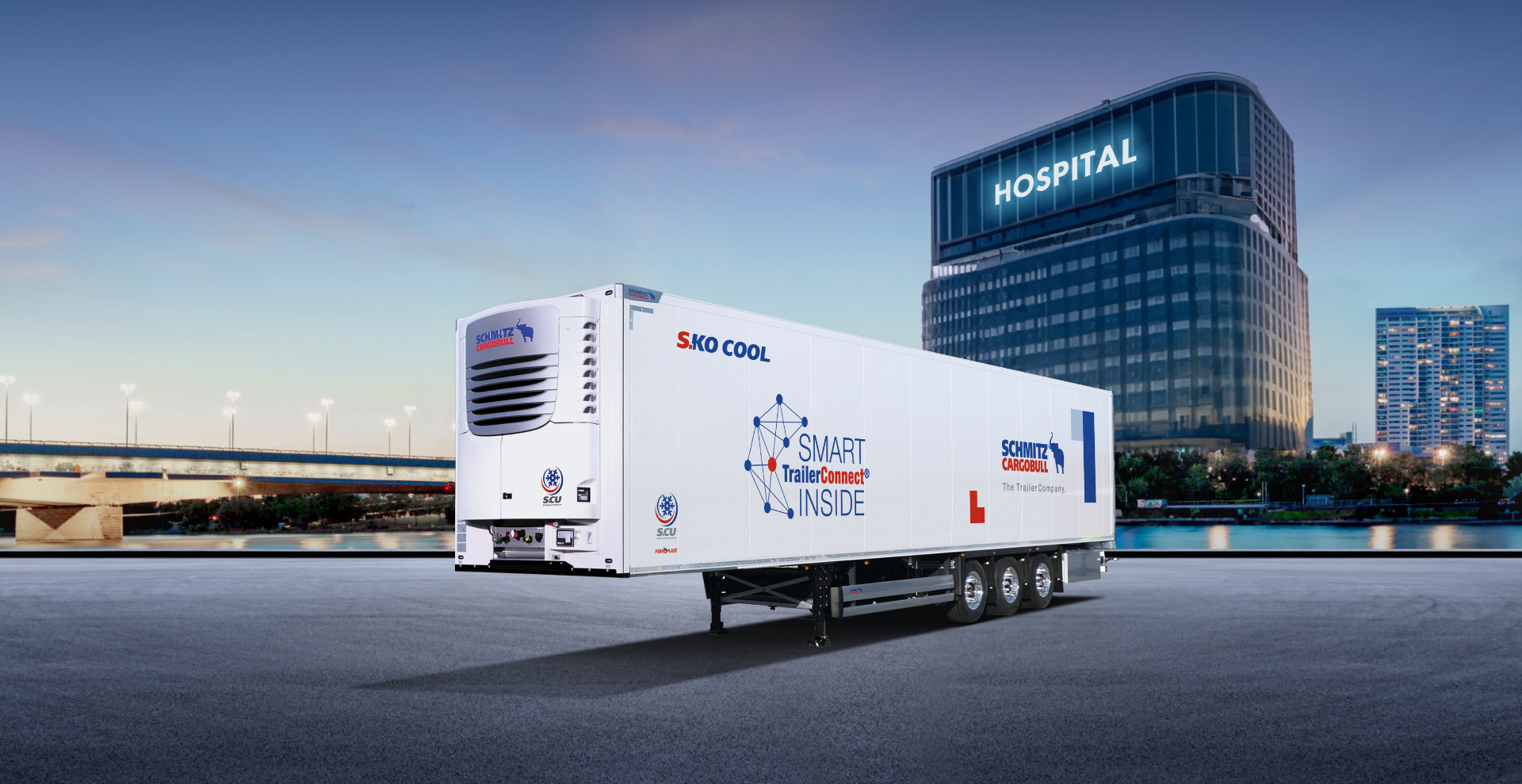
The products of the pharmaceutical industry are precious. The value of a single pallet of medicines, vaccines, or human adhesives can quickly break the million-euro barrier. Here in Germany, medicines worth around €60 billion are exported every year and almost €40 billion are imported. Too much money to allow medicines to become ineffective or even dangerous for patients due to incorrect storage or improper transport. The industry has long recognised this and has successively raised the requirements for services relating to this sensitive cargo.
Useful GDP certificate
EU Directive 2013/C68/01 Good Distribution Practice (GDP for short) for medical products in human medicine has been enforced throughout Europe for ten years. The requirements for medicinal products do not end after production, packaging, and packing. Patients must be able to be sure that the quality of their medicines is maintained throughout the entire supply chain. The GDP regulations presented on 7 March 2013 are intended to ensure that quality is also maintained in distribution and are directly linked to the GMP (Good Manufacturing Practice) guidelines for manufacturing practice.
Protection against falsified medicines
In addition to quality assurance in the transport of high-quality pharmaceutical, medical, and medical technology products, the regulation for good distribution practice also serves to protect against falsified medicines in the legal supply chains. All companies involved in the value chain, such as manufacturers, wholesalers, pharmacists, and logistics providers of pharmaceutical products, must comply with the directive and regularly subject their processes to GDP audits. The focus is on distribution, safety, the cold chain, packaging quality and reliable, functional technology. Both shippers and transport and logistics service providers have been under greater obligation since the introduction of GDP. This ultimately has an impact on vehicle manufacturers, who must guarantee seamless temperature monitoring in the body. The industry makes a fundamental distinction between pharmaceuticals that are subject to cold chain requirements and those that are not. In the first case, this means that the specified temperature range must be ensured throughout the entire transport chain from the manufacturer to the end customer.
Vehicle requirements for pharmaceutical transport
The German Medicines Act also requires critical parameters to be monitored and recorded during storage and transport. To transport sensitive pharmaceutical products, the vehicle must fulfil certain requirements for the transport of medicines. The transport containers should be designed in such a way that the quality of the contents is not impaired. Only an ATP-FRC-certified, insulated vehicle body with high hygienic requirements for materials and workmanship can be considered for pharmaceutical transport. It must be easy to clean, comply with the specified temperature limits between minus 25 and plus 30°C and guarantee a homogeneous temperature distribution in the body.
Seamless temperature monitoring
Modern refrigerated vehicles are equipped with a telematics system that enables seamless and sustainable temperature monitoring and temperature recording via calibrated temperature sensors and calibrated temperature recorders distributed throughout the cargo area.
Powerful cooling units and insulated partition walls are essential for multi-temperature operation. The certified trailers and semi-trailers have a constant temperature in the cargo area, can be monitored around the clock, 365 days a year and offer the greatest possible transport safety. To ensure perfect transport, the vehicles must be regularly maintained, cleaned and disinfected. A sticker with a pharmaceutical certificate proves that the vehicle fulfils these requirements.
Schmitz Cargobull's answer to all these questions is the S.KO COOL with GDP certificate. The refrigerated semi-trailer fulfils all legally defined requirements for pharmaceutical transport. This is confirmed by certificates from Pharmaserv and the European Institute for Pharma Logistics GmbH (EIPL), among others. The advantage of pharmaceutical certification is that some of the work involved in type qualification of the trailers at the customer's premises is no longer necessary. In practice, qualification is ultimately required for each vehicle.
Ensuring process reliability
Various certificates such as DIN EN 12642 Code XL as proof of a specific body stability, ATP certification for an uninterrupted cold chain, HACCP proof of hygiene and TAPA certificate as proof of the transport safety of high-value goods are proof of usability. "Thanks to the certification of our TrailerConnect® trailer telematics system, our customers can present an important certificate for their GDP audits that attests to the high quality and safety of our products," says Boris Billich, Chief Sales Officer at Schmitz Cargobull AG. "With the certificate, we can guarantee and document full process reliability for customers across the entire process chain: From the recording of data in the trailer, through data storage, to display in the internet portal or forwarding in the interface for data transfer to third-party systems (API)."
Additional equipment for pharmaceutical trailers
The pharmaceutical trailers also offer customers optimum load securing systems, movable partition walls, practical air distribution systems for a uniform temperature in the body, and double-decker systems for high, flexible utilisation. Fully automatic door locking systems via geofencing and an additional alarm system on the trailer have a reassuring effect. Door sensors recognise whether the rear doors are open or closed. With the help of a door locking system, the rear doors can also be locked or unlocked remotely via telematics portals or smartphone apps. The stored alarms notify the dispatcher of any deviation from the predefined conditions so that an immediate response can be made if necessary.