Environmental effects in view
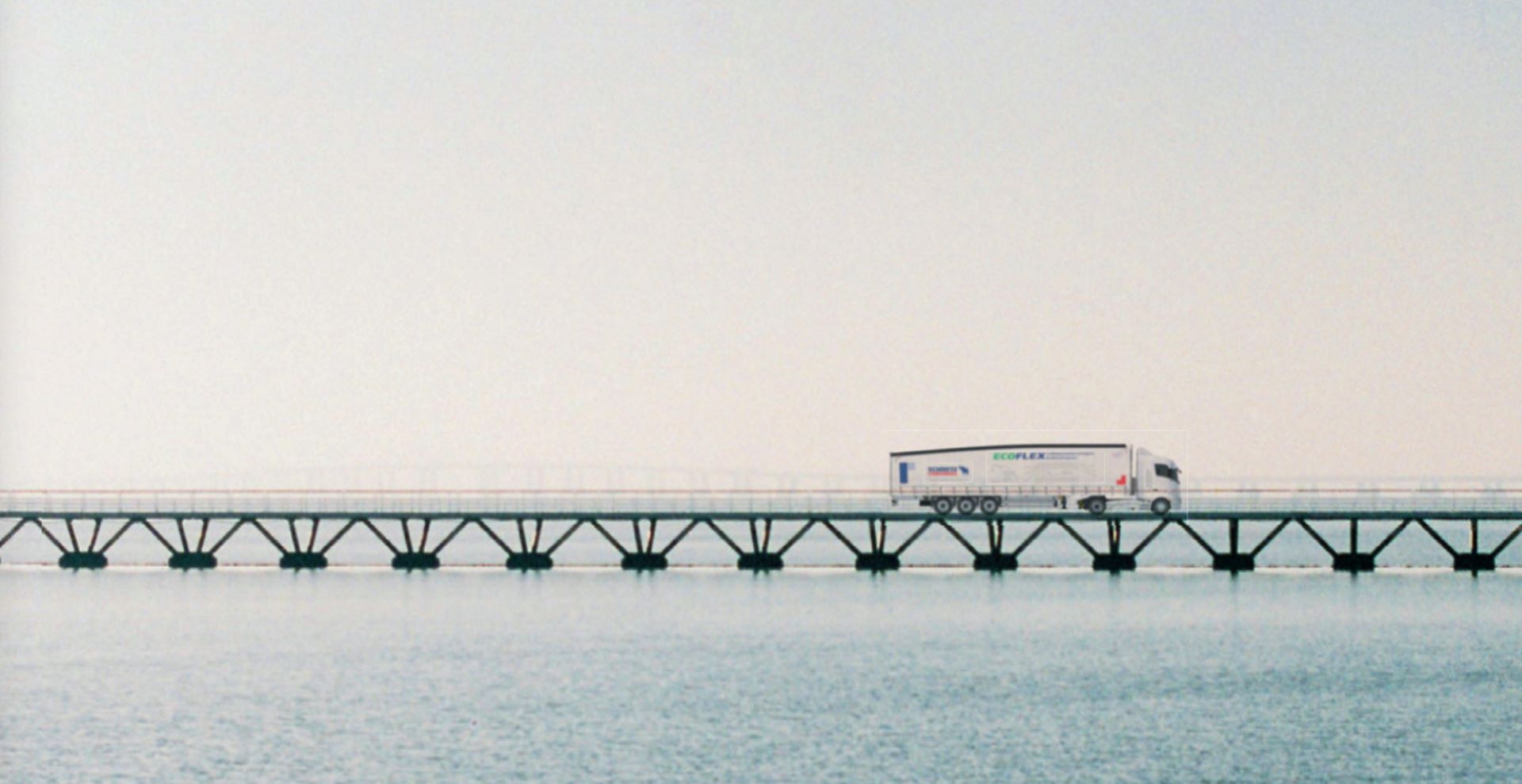
Careful handling of environmental impacts
Various auxiliary and operating materials used during the production process are subject to hazardous goods and hazardous materials regulations. This applies, for example, to paints, (flue) gases, greases, oils, adhesives or cleaning agents.
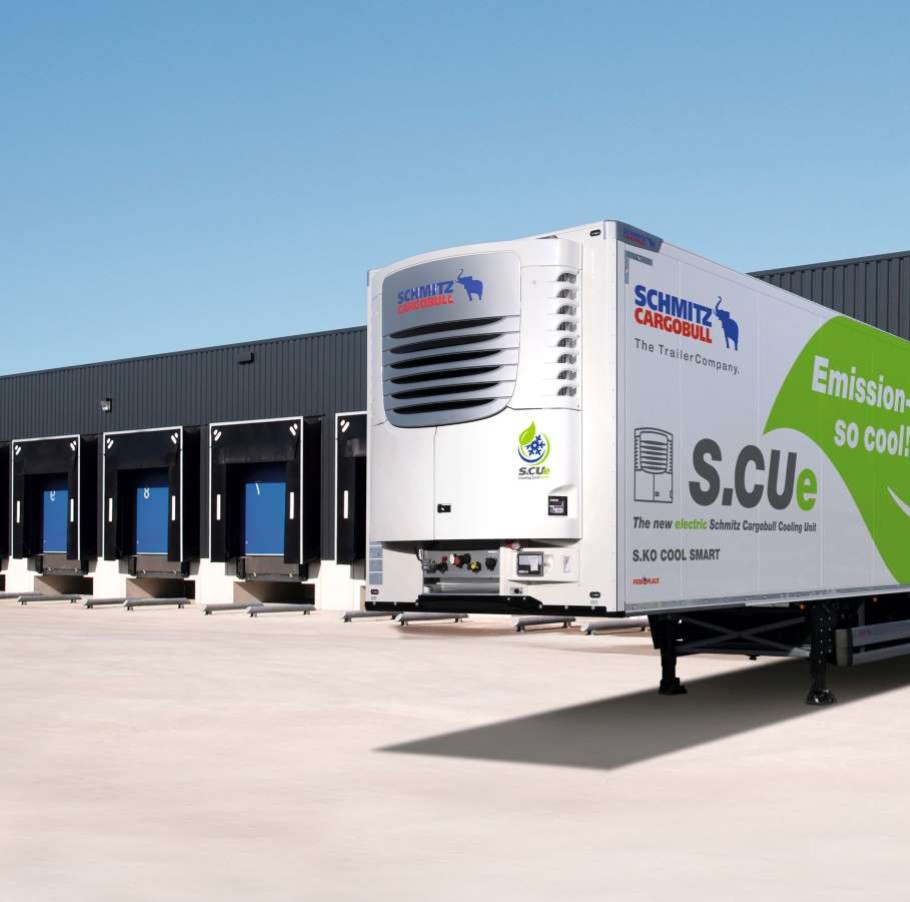
Managing our environmental impact
At Schmitz Cargobull, we work on key environmental issues across our production network. All major production sites are gradually introducing environmental management certification in accordance with ISO 14001.
Reducing energy consumption and emissions
Our goal is to reduce CO2 emissions per trailer by half by 2035. The zero measurement is currently being prepared on the basis of financial years 2019 / 20 and 2020 / 21. The values are being recorded step by step and specifications for implementation in the various plants are being drawn up.
-
Green power for other plantsFor other plants, the increased use of green power is on our agenda, as the project at our new factory in Zaragoza, Spain shows. In Altenberge, initial talks are being held with the energy supplier to supply the factory entirely with wind energy.
-
Green power for our factory in SpainIn 2022, Schmitz Cargobull commissioned a new plant in Spain. The plant in Zaragoza will be equipped with 2,300 sqm of solar panels on the roof. The electricity generated in this way will be used for production and the offices. The plan is to generate 700,000 kWh per year. Schmitz Cargobull has invested significantly in this project, we are planning annual cost savings in the five-digit range.
Careful approach to auxiliary and operating materials
At our production facilities, the waste is disposed of by professional disposal companies. The production at our plants uses many recyclable materials. Clean collection and separation as well as the reduction of production waste are essential starting points for establishing a circular economy.
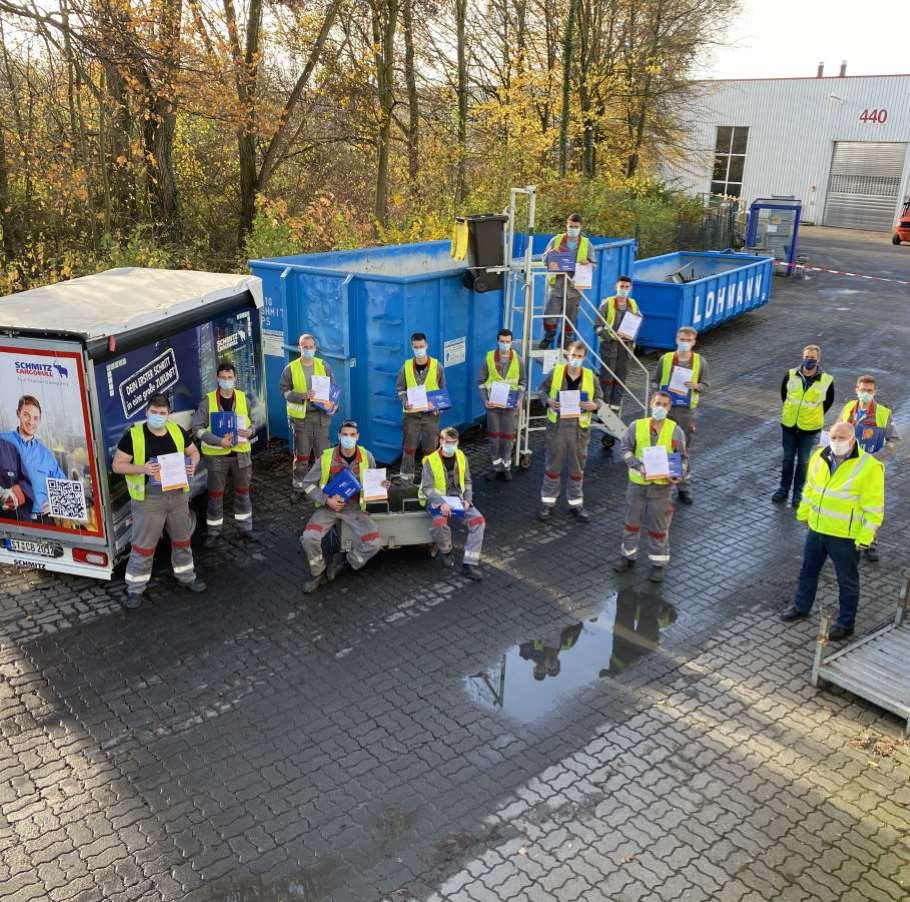
Clever clogs – Apprentices awarded safety prize
In November 2020, apprentices at the Altenberge plant were awarded the “Schlauer Fuchs” (“Clever Clogs”) safety award by the wood and metal workers association in Germany. Our apprentices developed a disposal system that improved occupational safety and ergonomics at work.
Efficient and environmentally conscious processes
-
Use of galvanisation instead of paint: Entire chassis are no longer painted but are galvanised instead. Galvanising materials increases their protection against erosion and improves their durability
-
Gluing instead of riveting when building insulated box bodies: Glued connections are more efficient than riveted ones as they create a flush join, thus reducing the amount of material needed.
-
Folding instead of screwing: Folding also creates a
flush join, offering a number of advantages compared to
point-to-point connections. While the strength of these
connections is higher, both their material consumption
and weight are lower.
-
Use of steel instead of aluminium wherever this makes sense. In terms of moment of force, steel is more efficient than aluminium, but the components still weigh the same. In our refrigerated trailers, we use steel to improve insulation.
-
Use of steel instead of plastic: In refrigerated trailers with large surface areas, steel is used to achieve a higher strength result and impermeability. Steel also has a particularly high reusage rate.
-
Bolting instead of welding: Bolting allows joined parts to be repaired as needed. No parts need to be disconnected from welded assemblies, welded back in again before being primed and painted. Galvanised parts can also be easily replaced for repairs thanks to bolted connections.